Independent floor insulation in a wooden house
In any private house, the main sources of heat loss are the roof and floor. Timely insulation of the floor in a wooden house will significantly reduce heat loss, improve the microclimate and reduce costs heating dwellings. Depending on the material of the supporting structure, the type of foundation, glazing area and architectural features, various methods of thermal insulation measures are used. This publication will tell you how to insulate the floor in a wooden house with your own hands, and what materials to use for competent thermal insulation measures.
Thermal insulation schemes for the floor of a wooden house
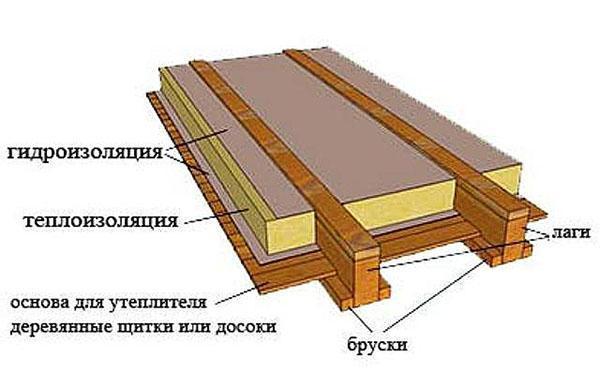
- Insulation of the floor in a wooden house from below (from the basement side) is carried out in the presence of a technical room, a basement floor or a cellar.
- Thermal insulation from the side of the premises is carried out if the house has a low underground or stands on a monolithic slab.
Next, we will consider the available insulation schemes for each of the above structures of a private house.
Thermal insulation of a wooden floor from the basement side
The technology for insulating the floor of a wooden house from the basement floor is as follows:
- Dismantle the subfloor to access the logs.
- Inspect the condition of the beams, clean them of debris for good access to the clean surface.
- Fasten a vapor barrier membrane, Izospan, around the entire perimeter of the ceiling. When using roll materials, the width of the strips overlapping each other should be at least 100 mm.
- Install a "cranial" beam on the side walls of each log, which will be a support for the insulation and create the necessary ventilation gap between the finished floor and the heat insulator. The recommended section of the cranial bar is 30x30 mm.
- Prepare insulation. The ideal option for this scheme is mineral wool slabs. The thickness of the heat insulator is selected in accordance with the height of the log. The width of each fragment should be 20 mm wider than the width of the space between adjacent lags (steps) to prevent the appearance of "cold bridges". If the use of polystyrene (polyurethane foam plates) is supposed to be used as a heat-insulating material, then the width of the fragment must clearly correspond to the step of installing the lag.
- To fix the material, stuff a transverse strip onto the timber. If polystyrene (penoplex) is used, then fill with polyurethane foam all the gaps between the insulation and the logs.
- On top of the heat insulator (in the case of using polystyrene foam) or along the transverse counter-rails, fill a layer of waterproofing: plastic film, roofing material, etc.
It remains only to close the space with a topcoat (waterproof plywood, OSB sheets, boards, etc.) and the warm floor in a wooden house is ready.
The method of insulating a wooden floor from the side of the room
The complexity of the implementation of such measures lies in the mandatory dismantling of the final flooring to gain access to the underground and the support bar (lags).
If the finished floor is made of grooved floorboards and is in good condition, it is recommended that each be numbered when dismantling to make it easier to re-install the material.
So, how to make a warm floor in a wooden house from the side of the home? The process of installing thermal insulation is relatively simple and is very similar to insulation from the side of the cellar, but only in the reverse order:
- Dismantle the finished floor. Attention should be paid to the construction of the "sex cake.
- Carefully inspect the condition of the support bar. Rotten areas need to be cut and replaced. This is done as follows: in place of the removed fragment, a part of the "healthy" beam is installed and fixed with metal corners or a channel of a suitable size. The overlap on the log should be at least 500 mm on each side.
- On the lower edge of each log, stuff a "cranial bar" with a side section of 20-30 mm.
- Make a subfloor. To do this, lay between the lags (do not fix) boards or wooden shields, the edges of which will rest on the cranial beam. Be sure to treat the entire resulting structure with an antiseptic! The recommended material thickness is 30 mm.
The length of each fragment of the subfloor should be less than the step of installing the lags by 10-20 mm.
The rest is simple. Layers are laid on the subfloor: waterproofing, heat insulator, vapor barrier membrane, counter batten (to create a ventilation gap), final flooring.
As you can see from the instructions, insulating the floor of a wooden house outside the room is a fairly simple process, but laborious. Next, consider another common scheme of thermal insulation measures, in which there is no need to dismantle the final flooring.
"Double floor": stages of work
This technology is suitable for timber structures erected on a monolithic concrete base.
It should be understood that installing a new warm floor on a wooden floor of a building will take from 12 to 20 cm of dwelling space, therefore this technology is used in rooms with "high ceilings".
- Remove the skirting boards and inspect the covering. If necessary, replace the fragments of the old flooring, seal the cracks with polyurethane foam.
- Install new logs with a step of 600-700 mm across the laying of the old support bar. Adjust their location so that the upper edges of the lag are strictly in the same horizontal plane.
- Cover the structure with a layer of vapor barrier membrane with an "overlap" on the walls of 100-150 mm.
- Place insulation between the new support beams. For such work, mineral wool heat insulators are most often used. The use of expanded clay would be a budget option.
- Lay a layer of waterproofing material on the insulation.
- Fill a counter-rail 15-20 mm thick on the new lags.
Install new flooring, which can be plywood, OSB sheets, tongue-and-groove floorboards and install skirting boards.
Underfloor heating system
One of the options for carrying out insulation measures is the creation of a "warm floor" system in a private house. There are several ways to implement this project.
Laying the heating element under the screed. This method involves the following work:
- leveling the base;
- laying a layer of heat insulator (foamed polyethylene, foam flon);
- heating element laying (cable, mats);
- reinforcement;
- finishing screed based on ready-mixed or sand-cement mortar.
It should be understood that far on each base will be able to withstand a mass of about 300 kg / m2... That is why the technology of creating a "warm floor" system in a wooden house without a screed is very popular among our compatriots. This design does not overload the floor and practically does not "steal" the useful space of the living space.
It should be noted that electrical systems must fully comply with all fire safety requirements and must not heat up over 27 ° C and have a power of no more than 10 W / m running cable.
The "warm floor" system is laid on a wooden base in the space between the joists. How to make a "warm floor" on a wooden floor with your own hands?
- Inspect the old base and repair if necessary.
- Install the logs on the wooden floor in increments of 60 cm.
- Place metal mesh and insulation between the joists. Layer thickness ¾ from the height of the log. The ideal option is foamed polyethylene with a metallized layer facing up.
- Unfold and fix the heating element on the grid, install the temperature sensor (in the corrugated tube).
- Lay the floor covering.
It is important to remember that the heating cable in electric systems "warm floor" should not be located closer than 3 cm from any wooden structures, including the topcoat.
Insulation for a wooden floor
Today, the domestic construction market offers a huge selection of thermal insulation materials, among which the most in demand are:
- Mineral wool insulation: slag, stone and glass wool. Any representative of this class has a number of advantages, among which experts note incombustibility, good sound and heat insulation characteristics, vapor permeability, low cost.
- Polyfoam is one of the most popular heat insulators in the budget segment. Lightweight, not hygroscopic, has excellent thermal insulation properties. Disadvantage: flammable, and when heated, it emits toxic fumes. A more modern and safer analogue of polystyrene is extruded polystyrene foam.
- Foil insulating material is an excellent material for most thermal insulation work. Does not absorb moisture, does not rot, is not flammable. Good performance at a sufficiently low layer thickness.
Another representative of "new technologies" is polyethylene foam (penofol), which has the same advantages as Isolone. There are types of foam foam with a self-adhesive side, which facilitates the installation of the material during repair and construction work.